Palletizing
Function
Using template programs, just set the initial pick and place positions, product dimensions, number and spacing, to complete the programming of the palletizing process.
Advantages
Operated on the teaching programmer, supporting software for palletizing tasks. Helps shorten setup time, improving operation efficiency.
.Automatically generates palletizing programs.
.Easily check the status of palletizing.
.Easily select and change operation contents.
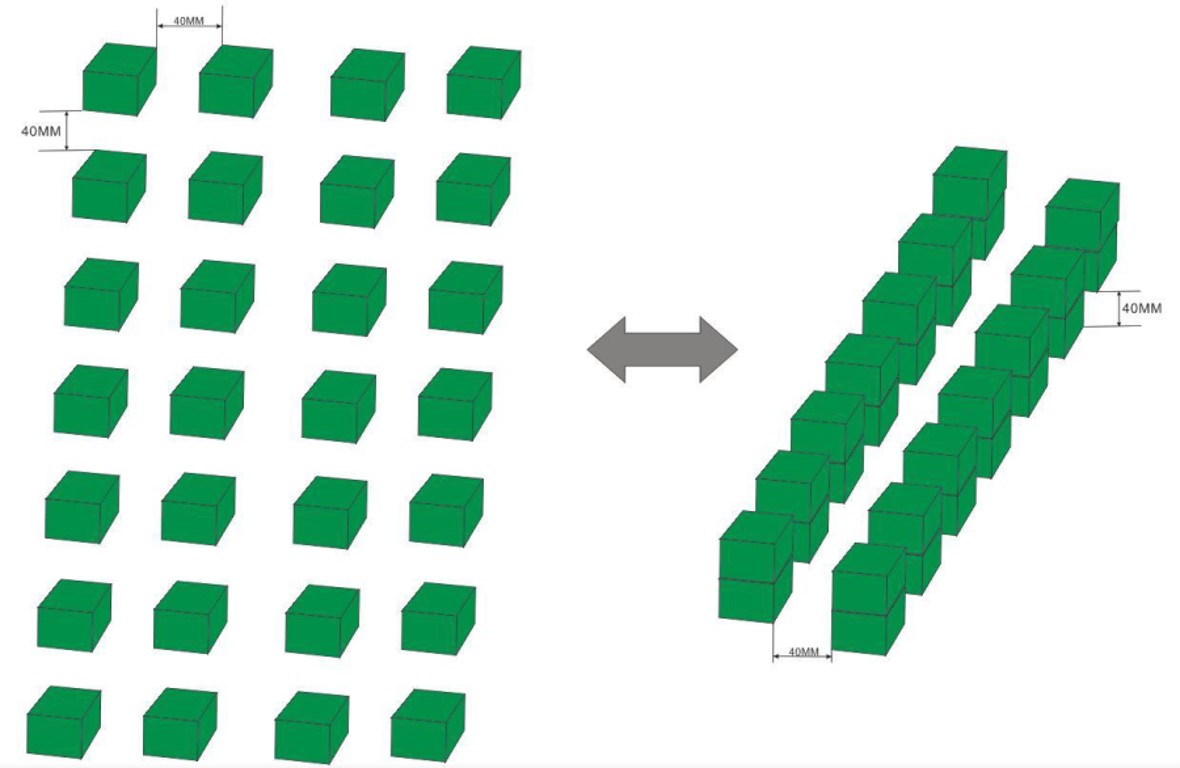
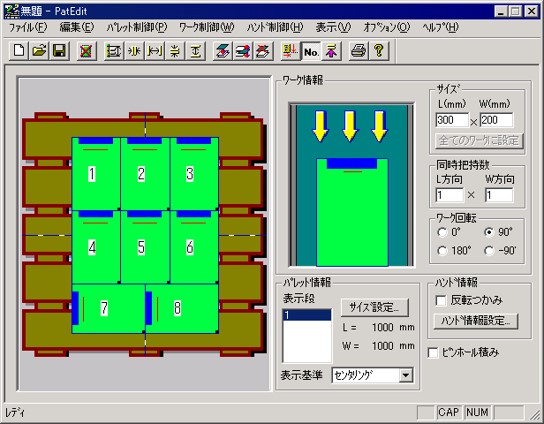